00.
PROJECT DETAILS
Role
Mechanical Design Intern
Tools/Skills
Product Design
Creo CAD
Product Management
Creo CAD
Product Management
Timeline
Jan - Apr 2023
Team
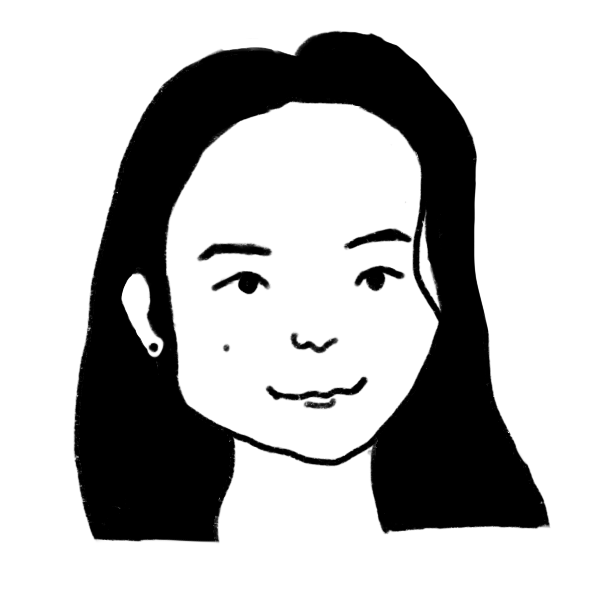
Me
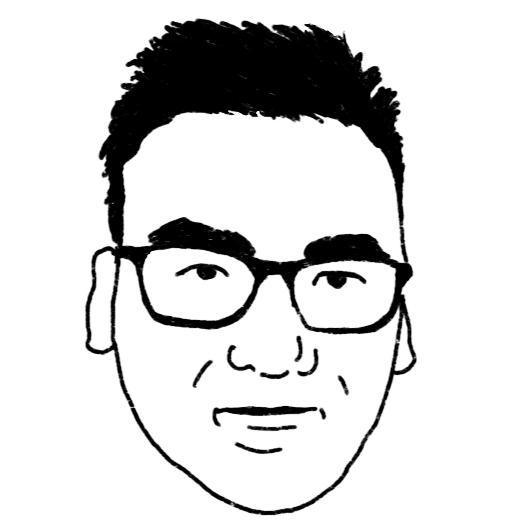
Thai
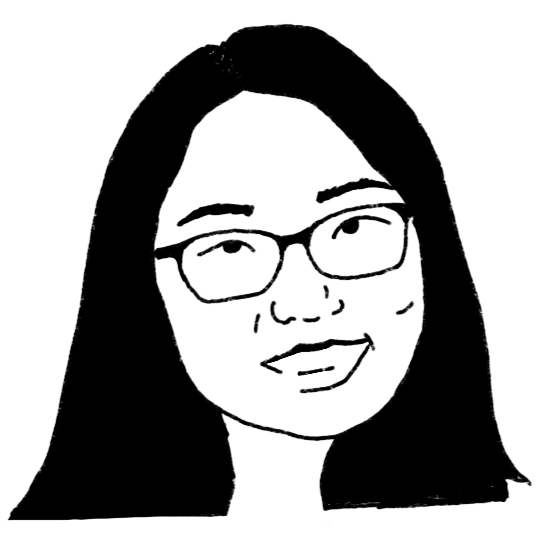
Mina
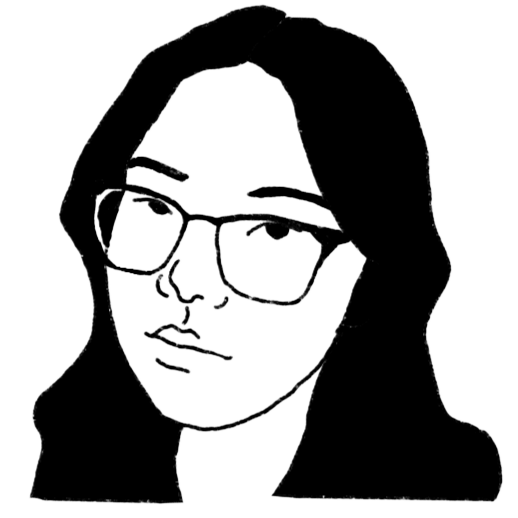
Nancy
01.
CONTEXT
SnapPea is a design strategy firm that specializes in developing Internet of Things (IoT) solutions for businesses. During myco-op term, I was primarily involved with an internal project for a gas sensor developed to monitor patient and infant bowel movements.
My specific tasks included:
My specific tasks included:
- printed circuit board assembly (PCBA) layout & enclosure design
- device accessory ecosystem planning
- industrial/visual design
02.
BRAINSTORMING
Seamless integration of the device into the users' daily activities is essential for creating a satisfactory user experience to prevent of product abandonment. Hence, I aimed to unlock the device's compatibility with a diverse ecosystem of tools by considering standard measurements for wearable devices and furniture while ideating the device's implementation methods.
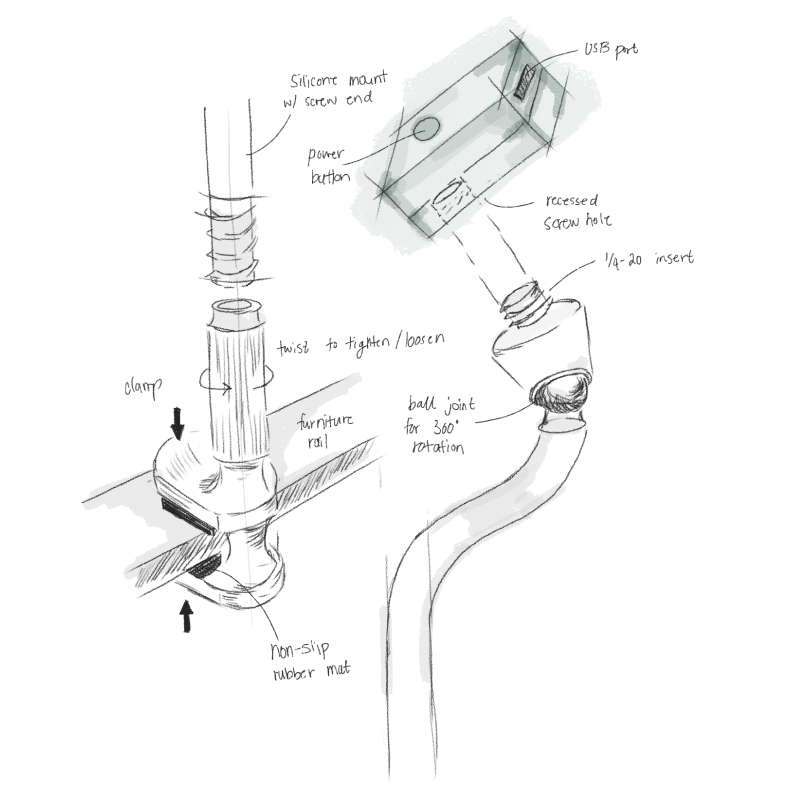
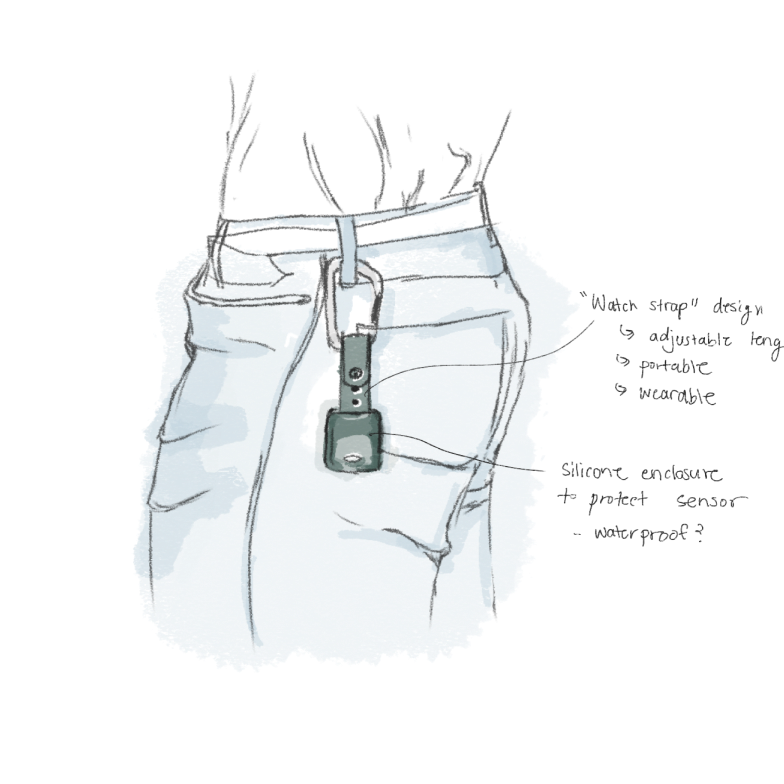
03.
REQUIREMENTS
The design of the PCBA enclosure was mainly driven by the mounting mechanism of the device in its operating environment. I worked closely with the team's industrial designer to ideate multiple implementation concepts in the form of wearable devices, clothing attachments, and furniture accessories.
At the end of our discussion, we had 8 design concepts. To identify the optimal solution, I created a ranking chart that compared the effectiveness of each concept based on the degree to which they fulfilled each requirement for a more quantifiable analysis.
At the end of our discussion, we had 8 design concepts. To identify the optimal solution, I created a ranking chart that compared the effectiveness of each concept based on the degree to which they fulfilled each requirement for a more quantifiable analysis.
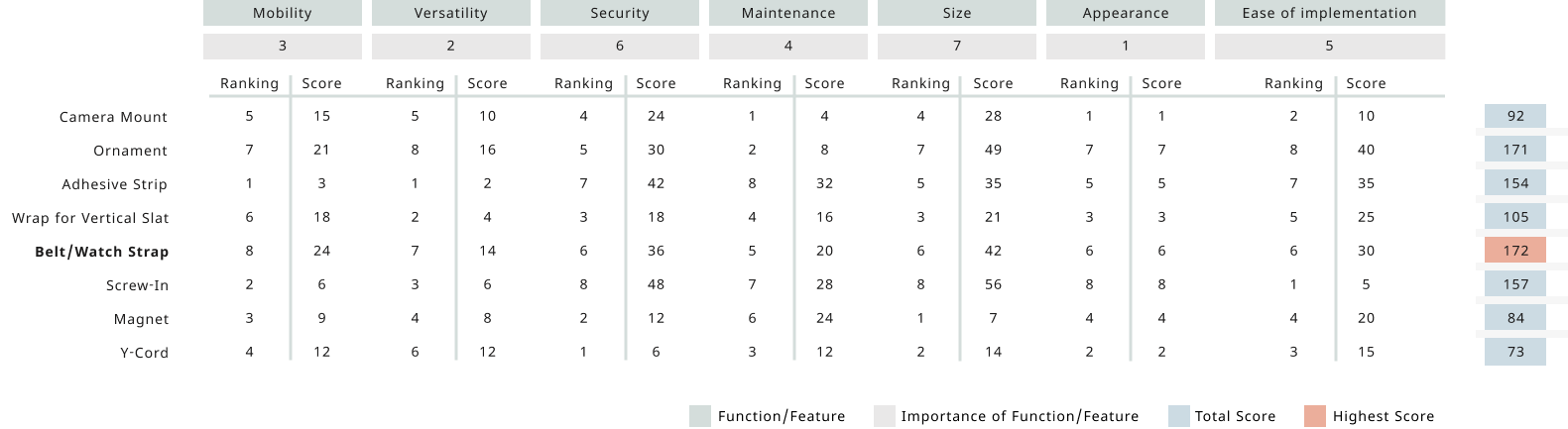
04.
HARDWARE COMPONENTS
To support the electrical functions of the device, I sourced the hardware components for both the device and wireless charging dock, which were then used to draft the PCBA layout.
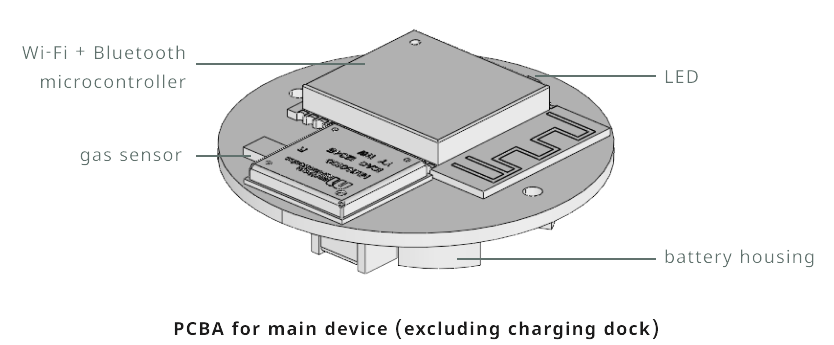
05.
INITIAL DESIGN CONCEPT
I first created a simple model for baseline testing to uncover both successful and ineffective features to inform subsequent design iterations.
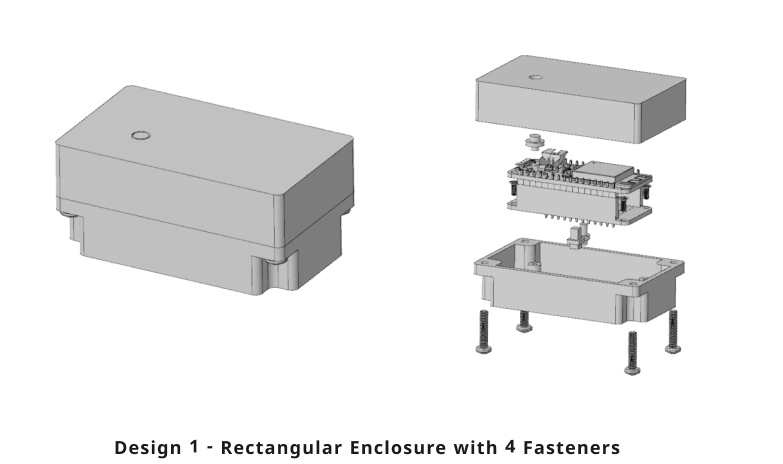
After 3D printing and assembling the prototype, I discovered two problems to target for the next design concept:
- Lack of flanges - no structural support during assembly & no seal between the two halves (risk of allowing dust, moisture, and other contaminants to reach the internal electrical component)
- Excess space inside enclosure created by screw bosses - violation of dimensional constraints
06.
DESIGN ITERATIONS OVERVIEW
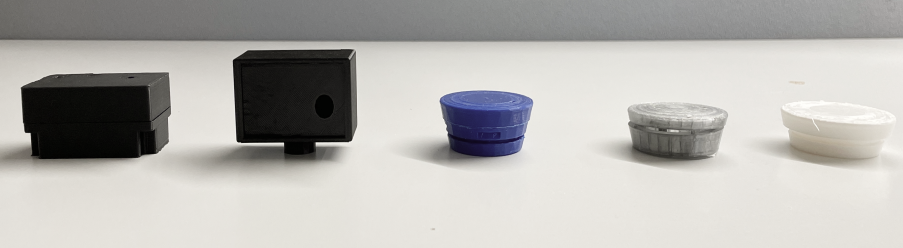
After the first concept, the model was modified multiple times to reduce the size and implement the ability to attach mounting accessories. The model eventually deviated from its original rectangular shape to a dome-like form to deliver a more organic and natural feel, enabling the product to blend more seamlessly into the surrounding environment
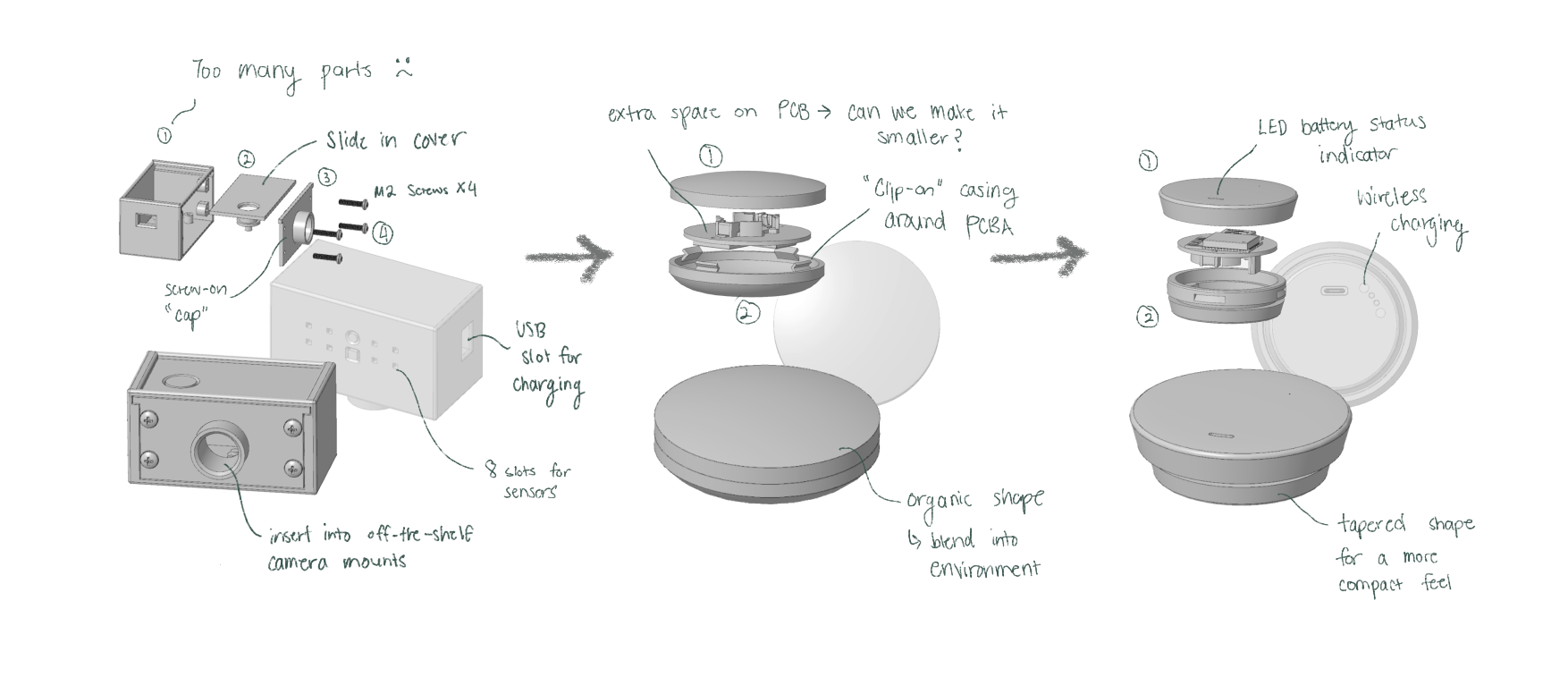
07.
MODIFICATION EXAMPLE
Removing interference in mating parts
Upon 3D-printing the third iteration, I discovered that the top and bottom housings could not be assembled due to an interference in the parts illustrated below. This meant that at the current stage, the product failed to provide full protection around the PCBA.
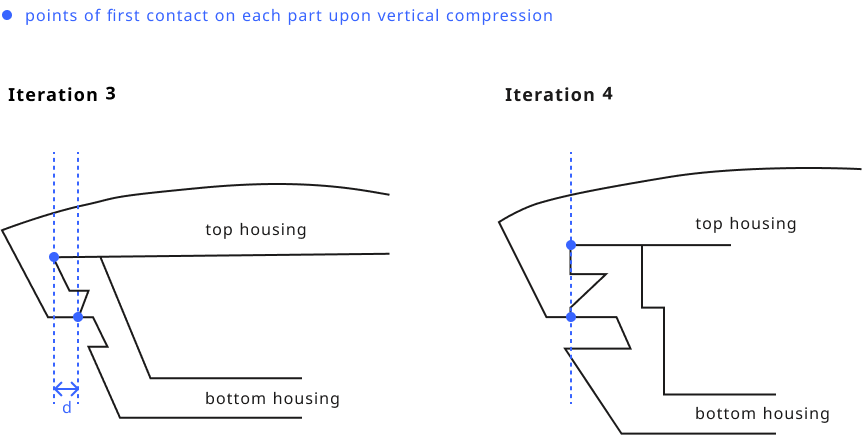
With the misalignment of the two points of first contact in iteration 3, the cantilever beam of the snap joint would need to bend an excess distance of “d". Since the print filament was made of polylactic acid (PLA), a rigid material with a minimal deflection range, the slanted wall caused the model to fail.
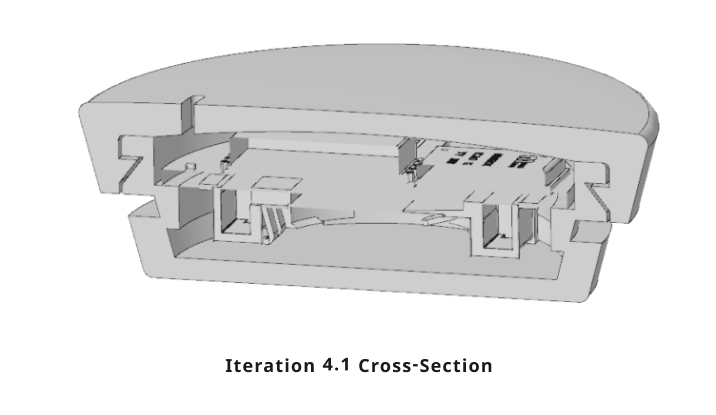
08.
LATEST ITERATION
Ver. 4.2
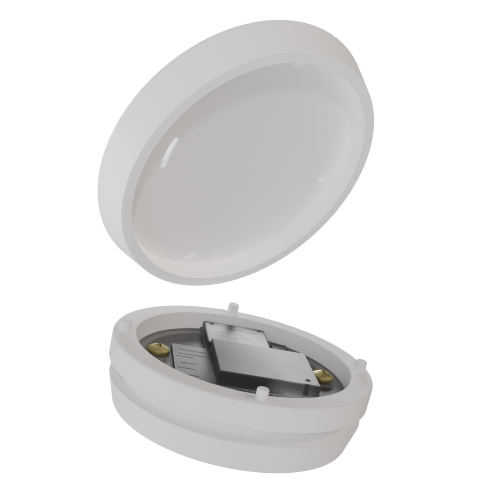
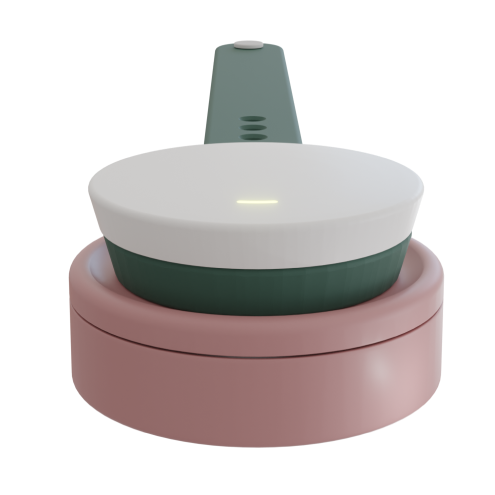
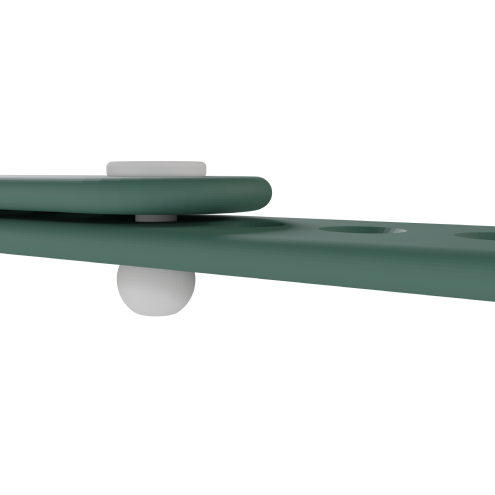
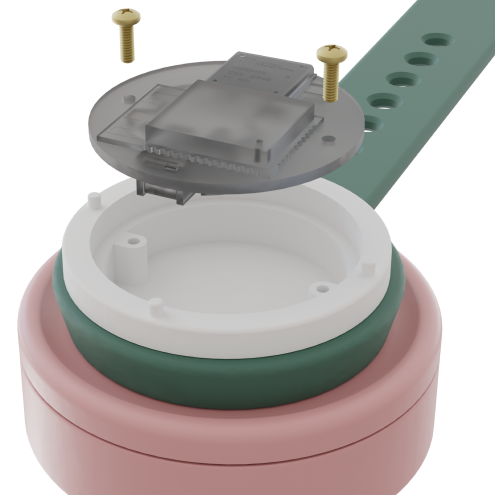
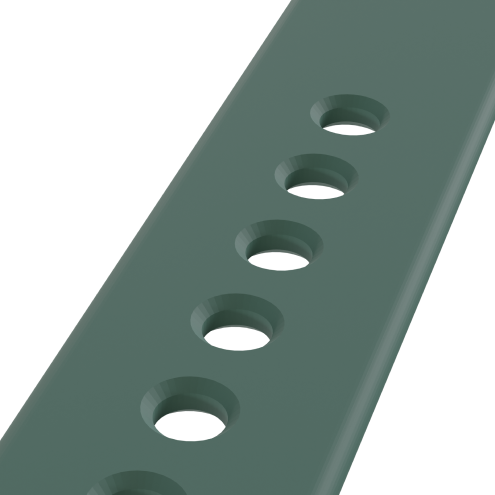
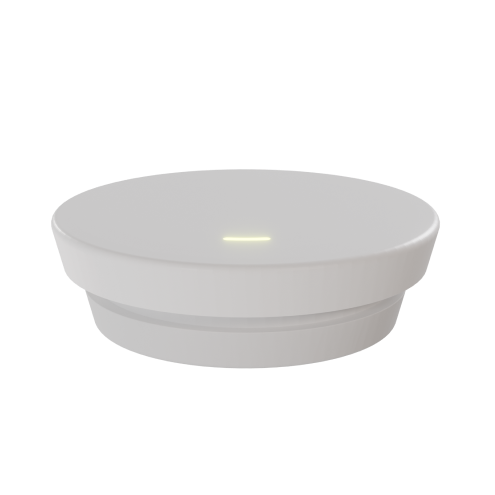
09.
PROGRESS RECORD
Throughout the course of the project, I evaluated each design iteration according to a set of goals I strived to meet in thedesign of my prototypes. This practice enabled me to assess the growth in my mechanical design skills based on the qualityof the prototypes created.
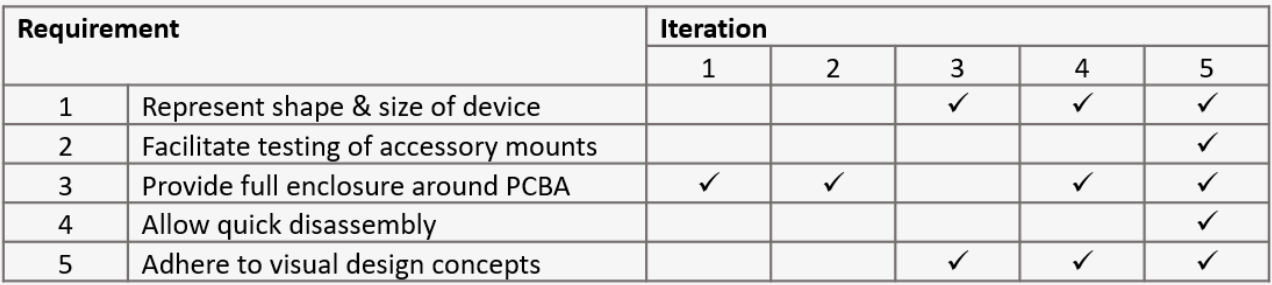
10.
NEXT STEPS
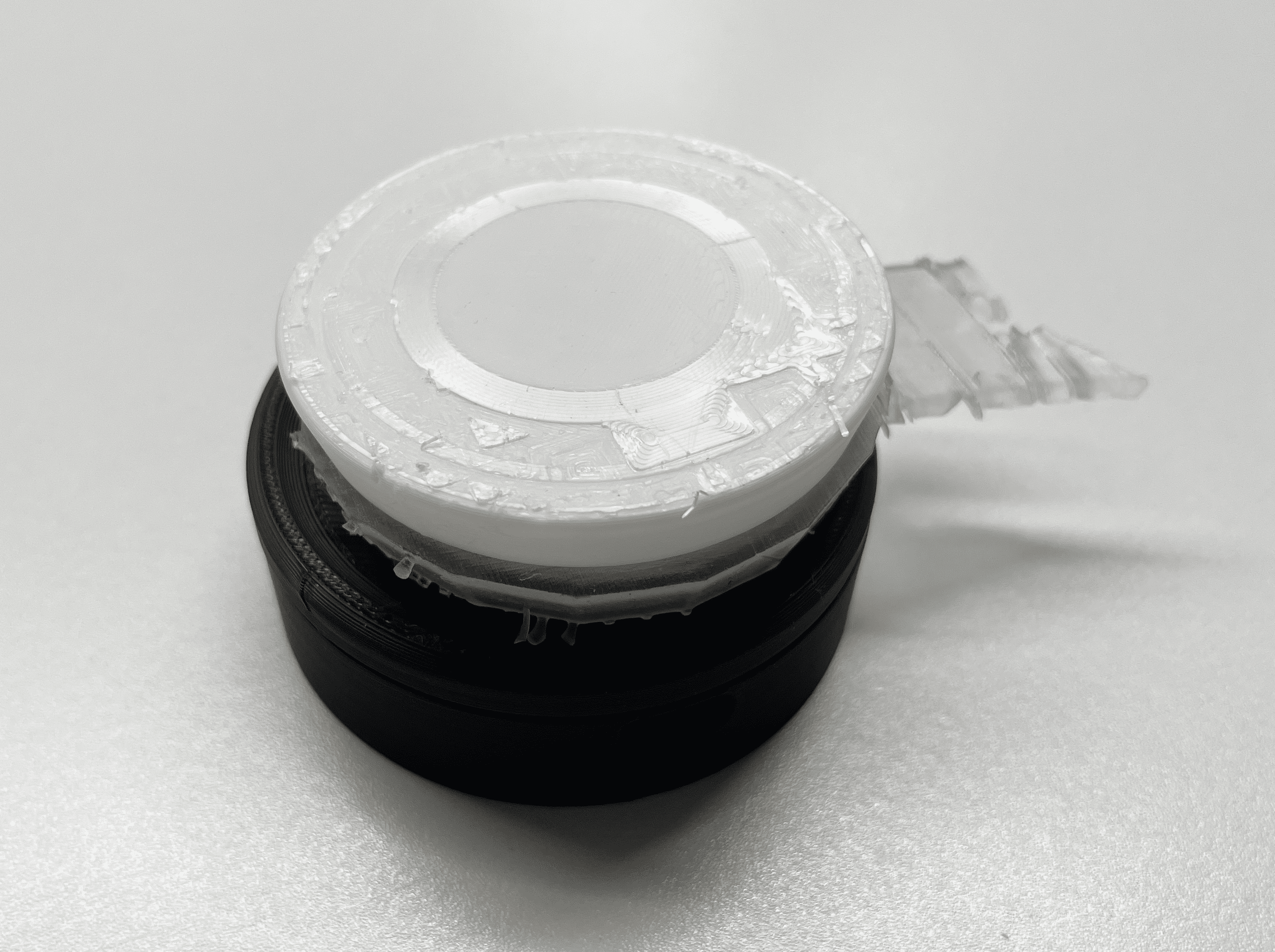